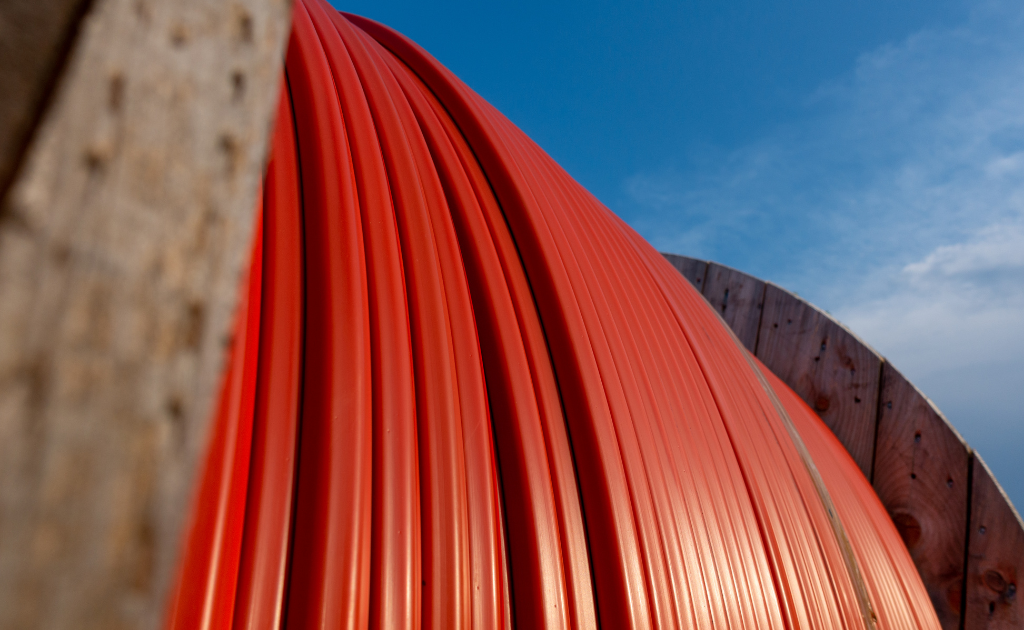
Tabla de Contenidos
- Introducción
- De paros por congelamiento a operación continua en zonas altoandinas
- De pérdidas por solidificación de producto a estabilidad térmica constante
- De consumo excesivo en recalefacción a eficiencia energética sostenida
- De mantenimiento correctivo frecuente a monitoreo preventivo eficiente
- De desperdicio de materias primas a procesos controlados en temperatura
- Conclusión
Introducción
El trazado térmico eléctrico ha demostrado ser una solución altamente efectiva para resolver problemas operativos en industrias peruanas que enfrentan condiciones climáticas desafiantes o procesos que requieren control térmico preciso.
Este artículo muestra cinco comparativas reales entre el “antes” y el “después” de implementar heat tracing en entornos industriales, destacando cómo su aplicación transforma la productividad, reduce costos y mejora la eficiencia operativa.
Son casos que ilustran el impacto tangible de una tecnología que, cuando se diseña e instala correctamente, cambia por completo el comportamiento térmico del sistema.
1. De paros por congelamiento a operación continua en zonas altoandinas
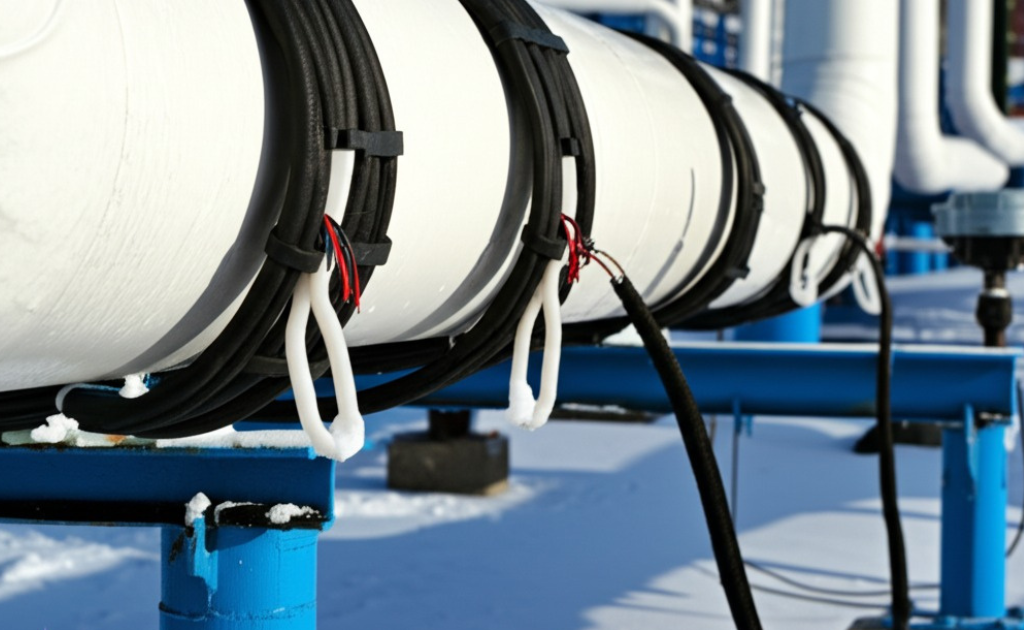
Antes: En una planta minera en la sierra de Arequipa, las tuberías de agua industrial sufrían bloqueos recurrentes cada invierno.
Estos eventos interrumpían el proceso de flotación, generando paradas no programadas de hasta 8 horas por semana.
Después: Con la instalación de un sistema de heat tracing autorregulante y aislamiento térmico en puntos críticos, se logró mantener las líneas libres de hielo durante toda la temporada fría.
Hoy, la operación funciona sin interrupciones térmicas, incluso con temperaturas por debajo de -5 °C.
Resultado: Más de 200 horas anuales recuperadas de producción, y una disminución del 90 % en los incidentes asociados al congelamiento.
2. De pérdidas por solidificación de producto a estabilidad térmica constante
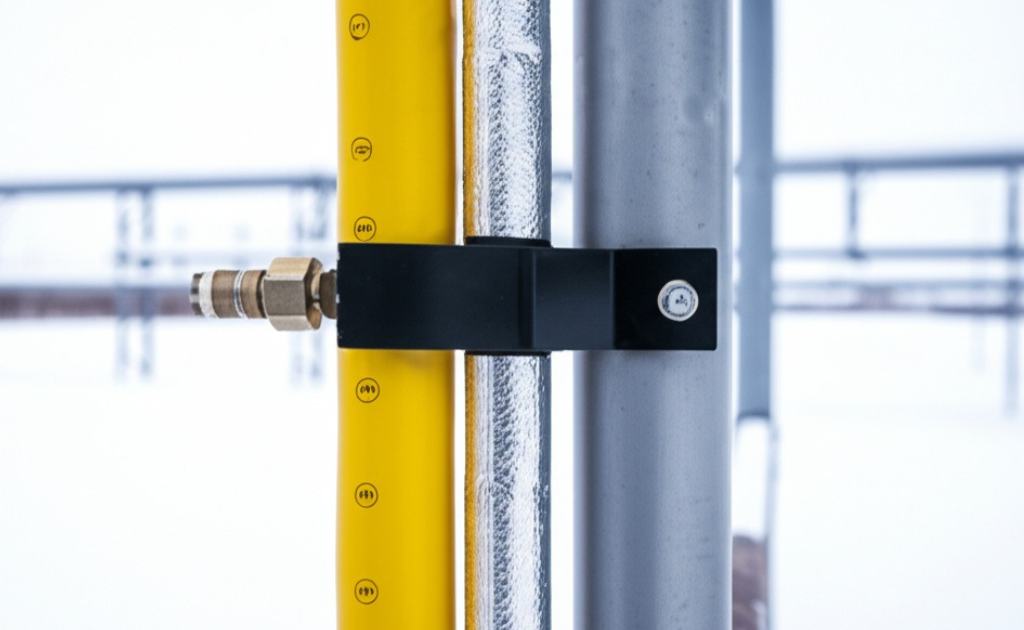
Antes: En una planta de alimentos en Lima, los conductos de chocolate líquido sufrían endurecimiento parcial durante la noche, obligando al personal a recalentar manualmente el sistema por las mañanas, con pérdida de producto y aumento del desperdicio.
Después: Se aplicó trazado térmico con controladores digitales y sensores PT100 en las líneas de producción, manteniendo el producto entre 35 °C y 40 °C las 24 horas.
Resultado: Eliminación del desperdicio por solidificación, mejora del flujo continuo del proceso y reducción de tiempo muerto al inicio de cada turno.
3. De consumo excesivo en recalefacción a eficiencia energética sostenida
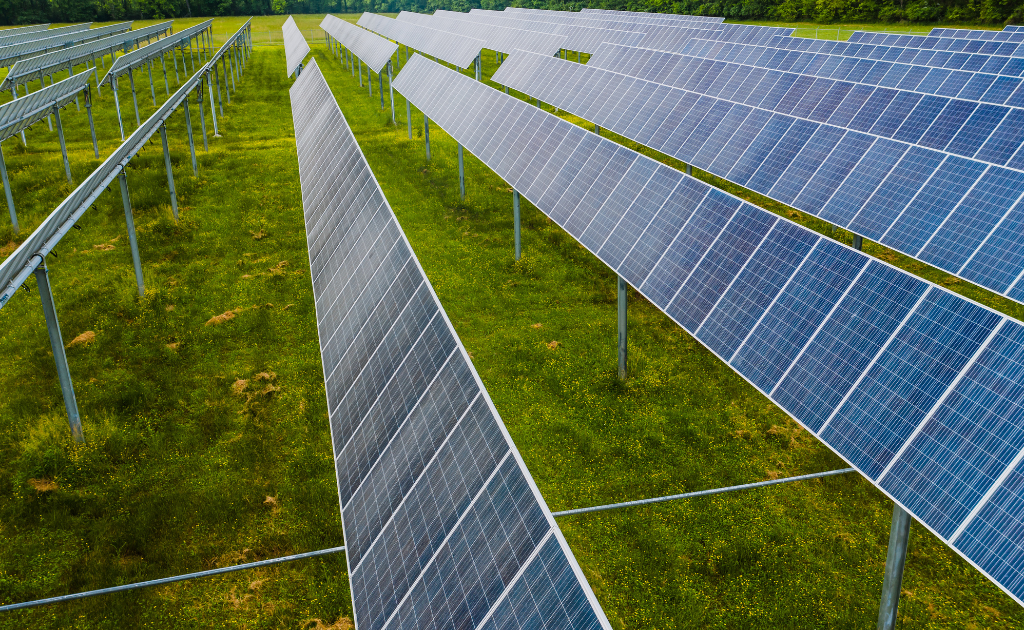
Antes: Una planta química en el Callao utilizaba resistencias eléctricas externas para recalentar tambores de materia prima, lo cual requería consumo eléctrico constante y generaba ciclos térmicos irregulares que afectaban la calidad del producto.
Después: Se reemplazó el sistema por cables calefactores de potencia constante con controladores por zona y mantas térmicas con aislamiento reforzado.
Resultado: Se logró una reducción del 30 % en el consumo energético, una mejora en la estabilidad de la materia prima y menos intervención manual para mantener la temperatura adecuada.
4. De mantenimiento correctivo frecuente a monitoreo preventivo eficiente
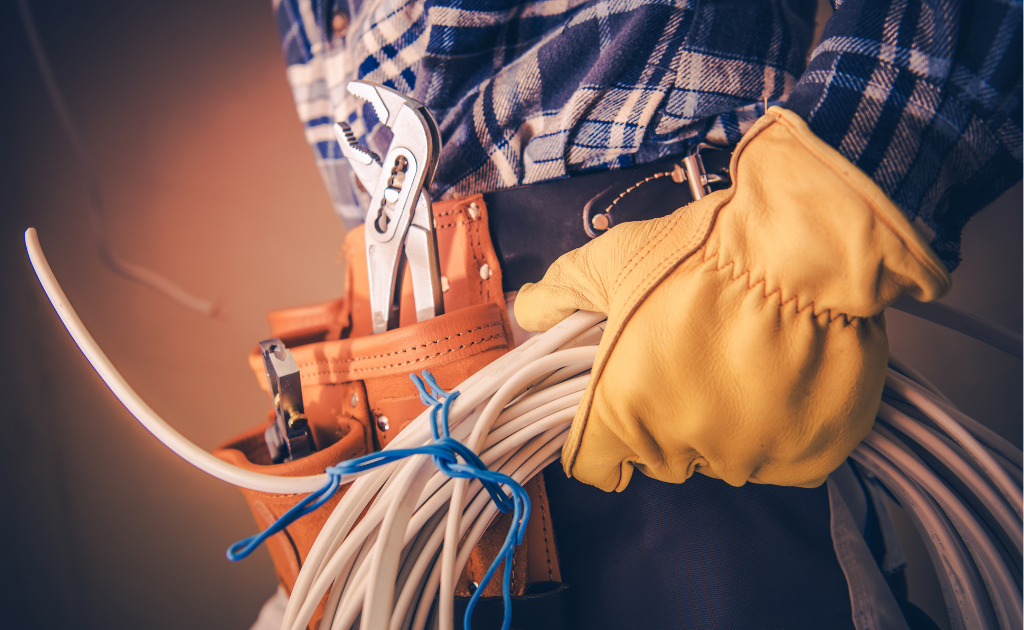
Antes: En una planta de tratamiento de aguas en Cusco, los operadores detectaban problemas térmicos solo cuando ya había una falla evidente (como hielo o pérdida de caudal), lo que implicaba reparaciones costosas y emergencias operativas.
Después: El nuevo sistema de heat tracing fue instalado con monitoreo digital remoto, permitiendo verificar en tiempo real el estado térmico de las tuberías y activar alertas en caso de desviaciones.
Resultado: Se redujo en más del 70 % el número de intervenciones correctivas, y el personal técnico ahora actúa preventivamente antes de que ocurran fallas críticas.
5. De desperdicio de materias primas a procesos controlados en temperatura
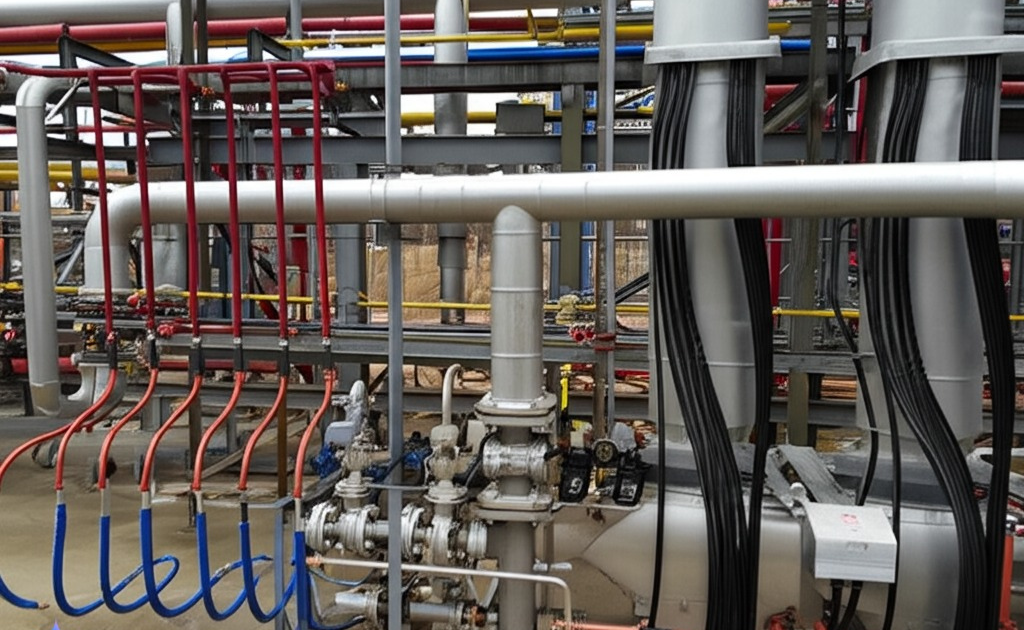
Antes: En un centro logístico de agroexportación en Ica, los tanques de almacenamiento de jarabe de maíz sufrían pérdidas de viscosidad por enfriamiento nocturno, generando sobrantes no utilizables o producto fuera de especificación.
Después: Con un sistema de trazado eléctrico en las paredes de los tanques y líneas de descarga, se logró mantener una temperatura constante de 45 °C, asegurando la fluidez del producto durante toda la jornada operativa.
Resultado: Reducción del desperdicio en un 60 %, mejora en la trazabilidad del producto y optimización del proceso de envasado sin interrupciones térmicas.
Conclusión
Estos cinco ejemplos reflejan con claridad el impacto real de implementar heat tracing en procesos industriales peruanos.
Desde evitar paradas hasta reducir consumo, pasando por proteger la calidad del producto, el trazado térmico no solo resuelve problemas, sino que optimiza operaciones completas.
Más allá de los beneficios inmediatos, esta tecnología representa una inversión estratégica en eficiencia, continuidad y seguridad operativa, especialmente en sectores donde la temperatura es una variable crítica.
Adoptar el heat tracing de forma planificada y técnica permite a las empresas en Perú alcanzar mayor confiabilidad, reducir costos ocultos y competir con procesos térmicamente estables en cualquier condición ambiental.