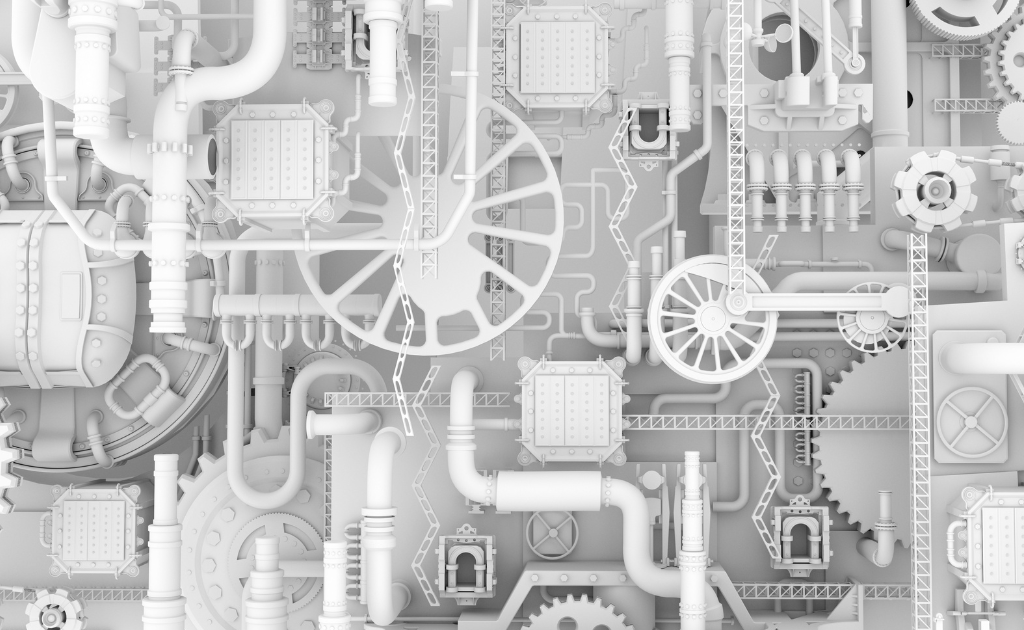
Tabla de Contenidos
- Introducción
- Rango térmico máximo y estabilidad de temperatura
- Complejidad en instalación y diseño de infraestructura
- Seguridad operacional en zonas sensibles
- Mantenimiento y confiabilidad del sistema
- Flexibilidad y adaptación a cambios operativos
- Conclusión
Introducción
En entornos industriales complejos donde se requiere mantener temperaturas elevadas o evitar la solidificación de productos críticos, las opciones de trazado térmico son diversas.
En especial, tres tecnologías compiten en eficiencia y adaptabilidad: el trazado eléctrico (heat tracing), los sistemas de vapor, y el trazado con fluidos térmicos como glicol o aceites especiales.
Este artículo ofrece una comparativa integral entre estos métodos, enfocándose en sus capacidades térmicas, facilidad de diseño, riesgos operativos y comportamiento frente a cambios en las condiciones de proceso.
Está dirigido a ingenieros y responsables de mantenimiento que buscan tomar decisiones informadas al seleccionar el sistema más adecuado para sus plantas, ya sea en zonas altoandinas, litorales o amazónicas.
1. Rango térmico máximo y estabilidad de temperatura
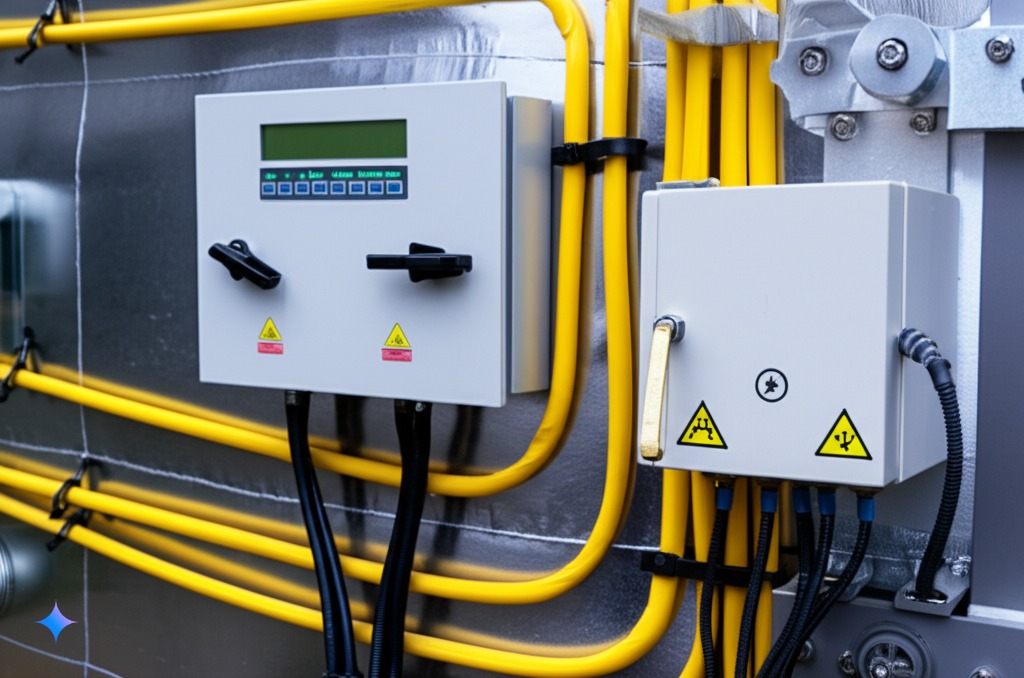
El trazado eléctrico con cables de resistencia mineral o potencia constante puede alcanzar temperaturas de hasta 425 °C, manteniendo una entrega térmica uniforme gracias al control electrónico en cada tramo. Esta solución es ideal cuando se requiere precisión en el rango térmico, como en líneas de polímeros, asfaltos o químicos sensibles a la temperatura.
El trazado por vapor, en cambio, puede superar los 250 °C dependiendo de la presión de trabajo, pero su control es menos preciso. Su eficacia depende de la calidad del condensado, la presión del cabezal y la eficiencia de las trampas de vapor.
Por su parte, los sistemas con fluidos térmicos pueden operar en un rango más amplio que el vapor, llegando hasta 350–400 °C con aceites térmicos de alta estabilidad. Sin embargo, presentan mayores desafíos en cuanto a control puntual, ya que dependen del caudal constante y la temperatura del fluido en circulación.
2. Complejidad en instalación y diseño de infraestructura
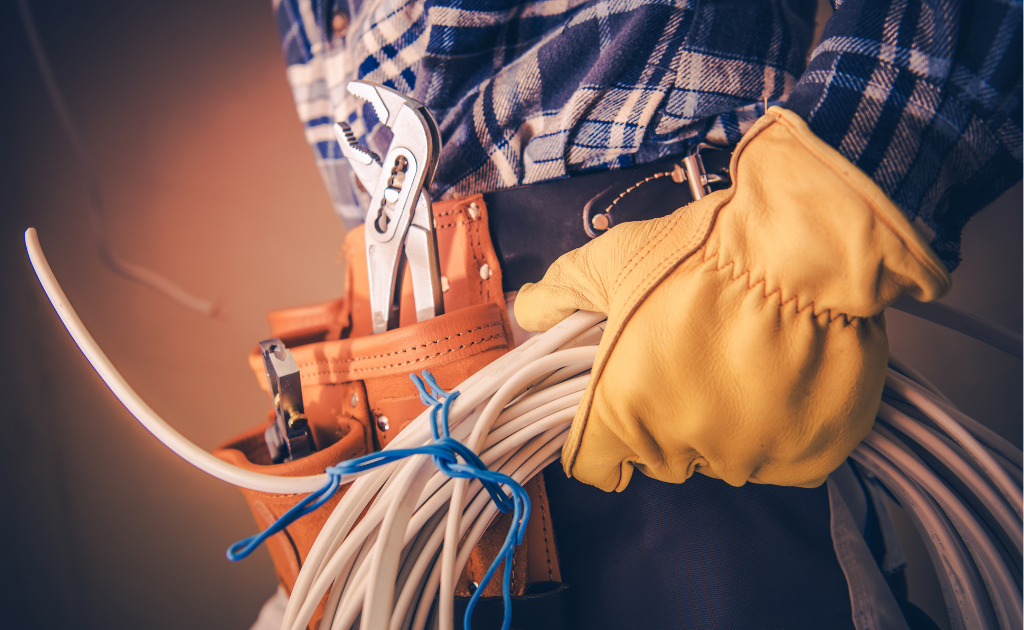
Desde el punto de vista de instalación, el trazado eléctrico es el más directo: solo requiere la distribución de cables calefactores, controladores y una fuente eléctrica adecuada.
Los diseños modernos permiten cortes a medida, autolimitación térmica y modularidad en el montaje.
Los sistemas de vapor implican una red de tuberías, trampas de condensado, válvulas de seguridad y aislamiento específico para altas temperaturas.
Esto representa mayor volumen de obra civil y coordinación mecánica.
El trazado con fluidos térmicos requiere bombas de circulación, tanques de expansión, tuberías resistentes a alta temperatura y estaciones de calefacción.
Este tipo de solución suele usarse en refinerías o procesos con gran densidad energética, donde el diseño inicial absorbe un alto coste de ingeniería.
3. Seguridad operacional en zonas sensibles
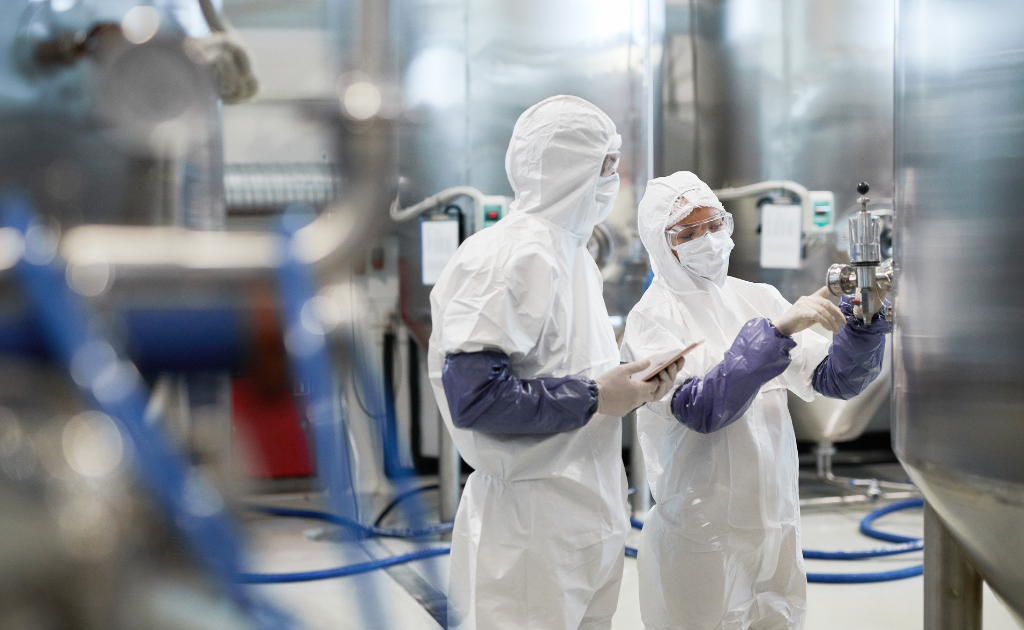
Los sistemas eléctricos deben cumplir normativas como IECEx o ATEX cuando se instalan en zonas clasificadas, pero pueden operar de forma muy segura si se utilizan cables certificados y cajas antideflagrantes.
Además, no presentan fugas ni presión interna, lo que minimiza el riesgo mecánico.
En cambio, los sistemas de vapor y fluidos térmicos implican presión, riesgo de fugas y quemaduras por contacto accidental.
Las fugas de vapor son una fuente crítica de accidentes en zonas confinadas, y los aceites térmicos pueden incendiarse si hay fallas en válvulas o sobrecalentamiento local.
Por ello, en industrias donde se prioriza la seguridad —como farmacéutica, alimentos o química fina— el trazado eléctrico suele ser preferido, aunque con un diseño y mantenimiento muy riguroso.
4. Mantenimiento y confiabilidad del sistema
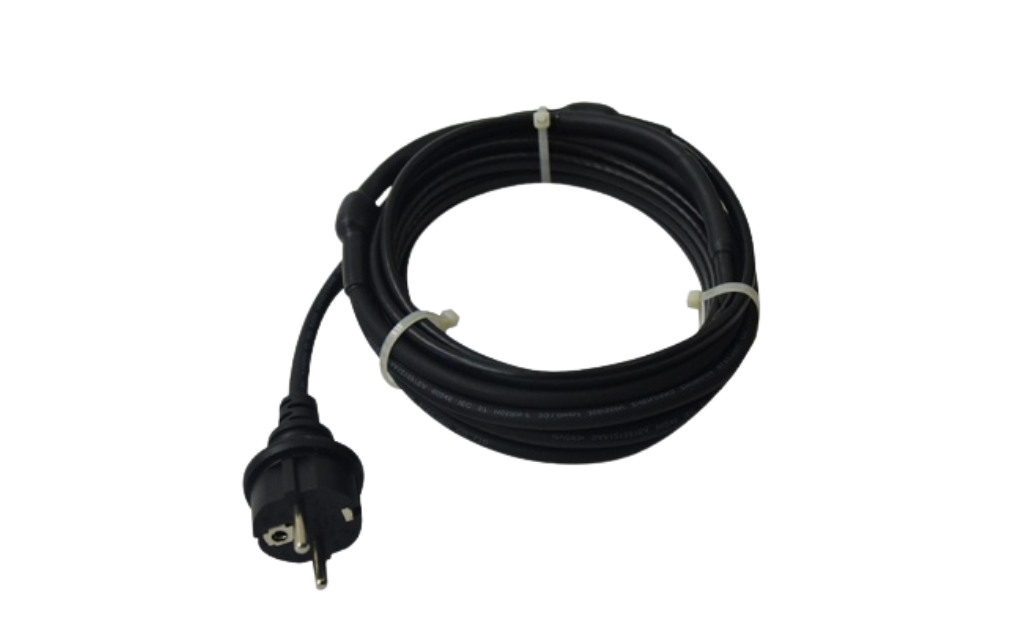
El heat tracing eléctrico tiene la ventaja de necesitar un mantenimiento relativamente simple: medición de resistencia de aislamiento, verificación de controladores y chequeo de continuidad. Si está bien instalado, puede operar más de 15 años sin intervención mayor.
Los sistemas de vapor requieren chequeos frecuentes de trampas, purgas, válvulas y presión. Una fuga pequeña puede traducirse en grandes pérdidas de energía o afectar toda una línea de producción.
Los sistemas con fluidos térmicos requieren monitoreo de calidad del aceite o glicol, mantenimiento preventivo de bombas y control de temperatura del depósito central. Además, si el fluido degrada su punto de inflamación, el riesgo aumenta progresivamente.
5. Flexibilidad y adaptación a cambios operativos
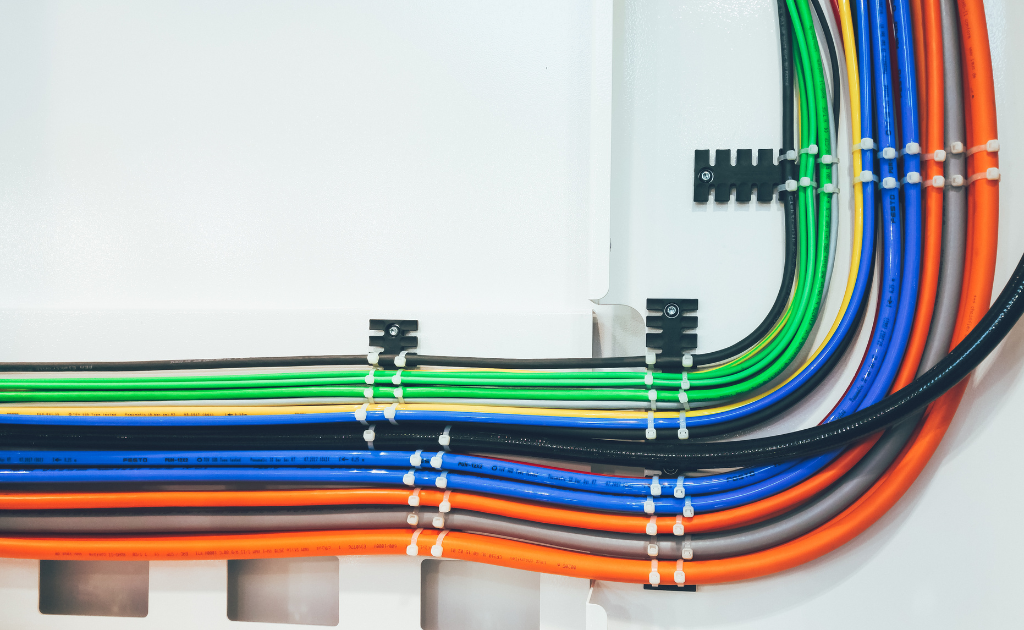
En plantas con alta rotación de líneas, cambios de producción o ampliaciones frecuentes, el sistema eléctrico es claramente más versátil: los cables pueden adaptarse a nuevas configuraciones, dividirse por zonas o integrarse a controladores SCADA fácilmente.
El vapor y los fluidos térmicos, en cambio, requieren redimensionar todo el sistema hidráulico o de presión cuando hay cambios de proceso. Esto implica cortes, paradas de planta y rediseño parcial del sistema.
En regiones del Perú donde la expansión industrial es progresiva y se requiere escalabilidad sin grandes inversiones adicionales, la adaptabilidad del heat tracing eléctrico representa una ventaja competitiva real.
Conclusión
Elegir entre un sistema de trazado eléctrico, uno por vapor o uno con fluidos térmicos no es solo una cuestión de temperatura, sino de visión de operación.
Cada tecnología tiene su nicho óptimo: el vapor sigue siendo útil en plantas que ya cuentan con infraestructura de calderas; los fluidos térmicos se adaptan bien a procesos con alta carga térmica sostenida; y el trazado eléctrico ofrece control, seguridad y versatilidad en entornos con necesidades variables.
En plantas ubicadas en Perú —desde la sierra hasta el litoral— el análisis debe contemplar no solo la eficiencia térmica, sino también la facilidad de instalación, mantenimiento, control ambiental y seguridad.
Con esta comparativa técnica, los responsables de planta podrán tomar decisiones mejor informadas al seleccionar el método de trazado térmico más eficiente y seguro para sus operaciones.