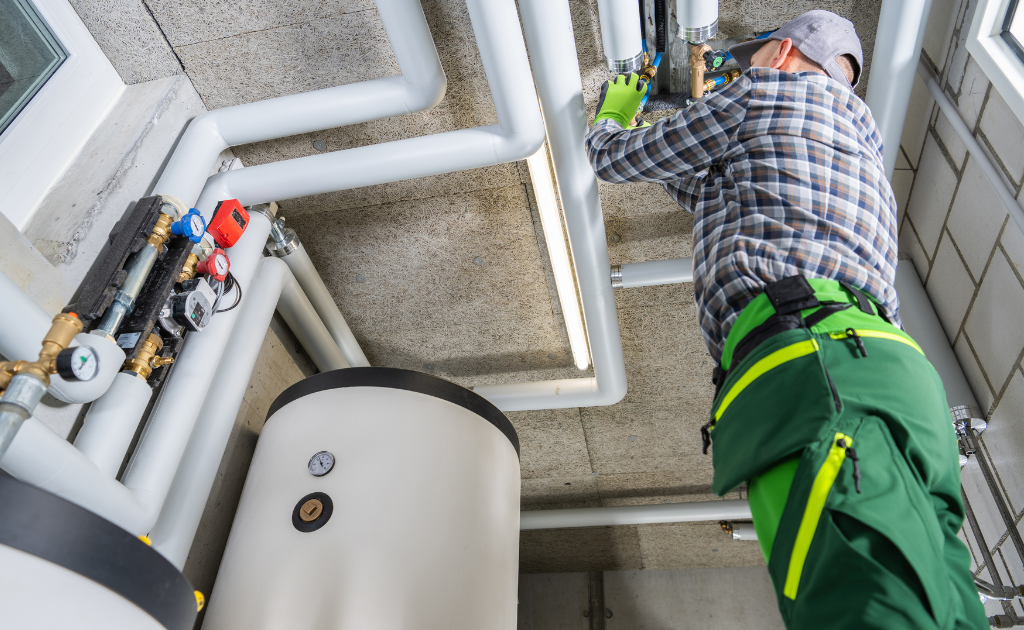
Tabla de Contenidos
- Introducción
- Temperaturas máximas sostenibles en procesos exigentes
- Eficiencia energética y control térmico preciso
- Mantenimiento operativo y confiabilidad a largo plazo
- Costo total de propiedad e infraestructura requerida
- Seguridad en zonas peligrosas y ambientes explosivos
- Conclusión
Introducción
En los sectores industriales peruanos donde se manipulan fluidos a temperaturas elevadas, como en la minería, petroquímica o alimentos, surge con frecuencia una pregunta crítica: ¿es mejor emplear un sistema eléctrico de heat tracing o utilizar vapor como fuente térmica?
Ambas tecnologías tienen capacidades térmicas elevadas, pero sus diferencias en control, mantenimiento y costo pueden hacer que una opción sea más viable que la otra según el proceso.
Este artículo presenta cinco comparativas técnicas esenciales que permiten entender cuál sistema se ajusta mejor a operaciones en Perú donde se requiere mantener temperaturas por encima de los 150 °C.
1. Temperaturas máximas sostenibles en procesos exigentes
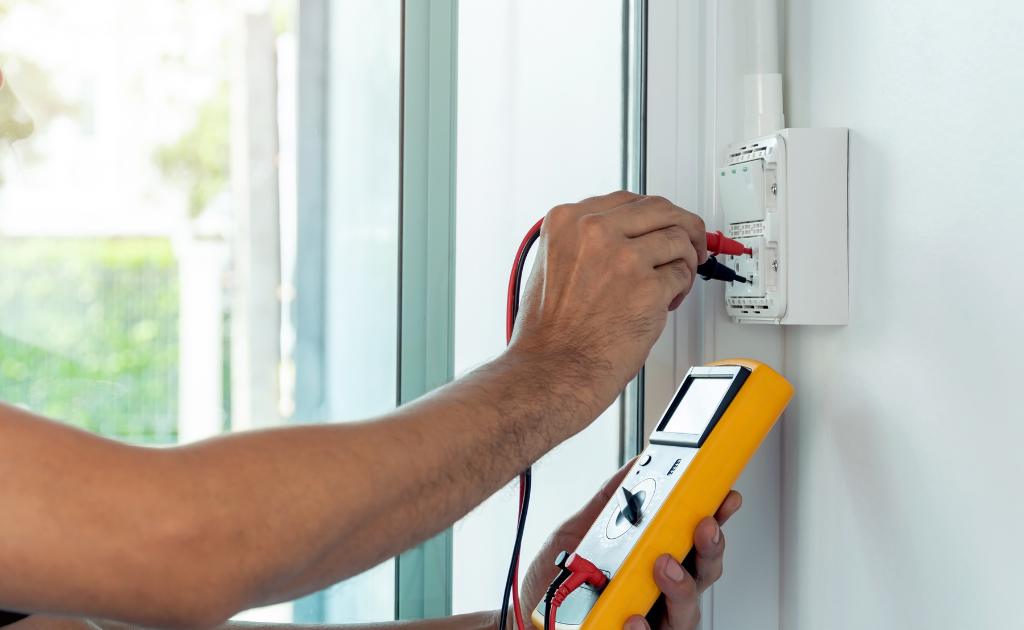
Los sistemas eléctricos de heat tracing pueden alcanzar temperaturas de operación superiores a los 400 °C cuando se utilizan cables del tipo mineral-insulated (MI), especialmente en aplicaciones de proceso como transporte de resinas, aceites pesados o sulfuros.
Esta capacidad es comparable a la del vapor, pero con mayor estabilidad en el control térmico.
Sin embargo, el vapor satura rápidamente el entorno del ducto a temperaturas que pueden llegar a 180–250 °C, y su poder calorífico, basado en la liberación de calor latente por condensación, es particularmente efectivo para procesos que requieren calentamiento inicial rápido.
En condiciones de gran altitud, como Cusco o Puno, donde la presión atmosférica disminuye, el rendimiento del vapor puede verse afectado, mientras que el heat tracing eléctrico mantiene una transferencia más uniforme, especialmente si se emplean cables de resistencia serie o skin effect.
2. Eficiencia energética y control térmico preciso
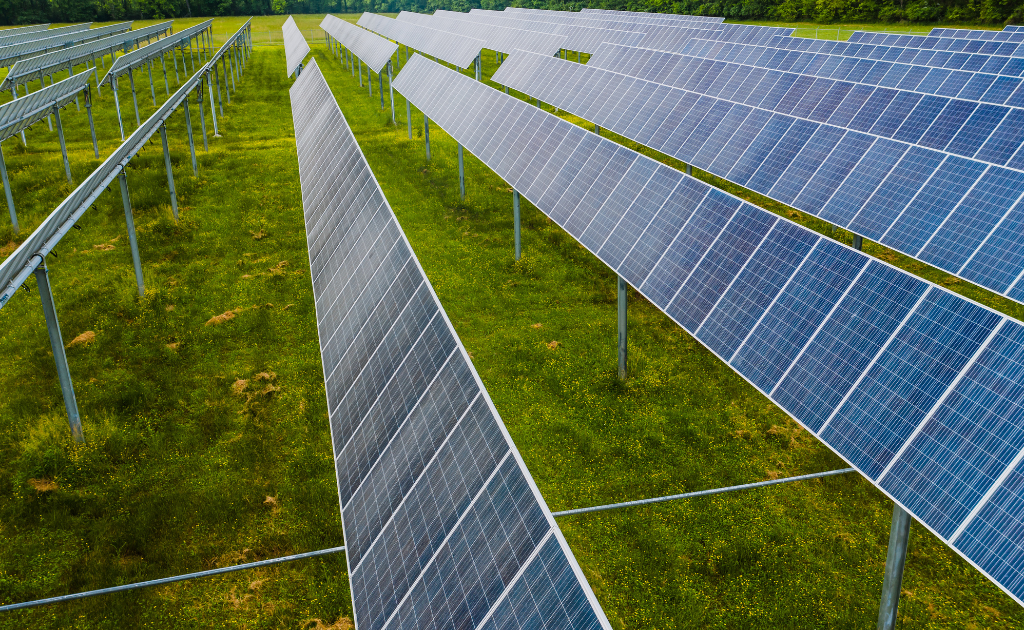
Una ventaja fundamental del heat tracing eléctrico es su capacidad de control: mediante sensores RTD o termostatos programables, puede mantener temperaturas con un margen de error mínimo, ideal para procesos donde pequeñas desviaciones impactan la calidad del producto.
En contraste, el vapor opera en modalidad de libre flujo (“free run”), con pocas posibilidades de regulación fina.
Esto conlleva un consumo muchas veces superior al necesario, generando desperdicio energético, especialmente cuando no se utilizan trampas de vapor o si estas presentan fallas.
Además, los sistemas eléctricos permiten cortes automáticos por zonas o monitoreo remoto, optimizando el consumo. Esto es muy útil en zonas donde la electricidad es más estable y económica que la generación o recuperación de vapor.
3. Mantenimiento operativo y confiabilidad a largo plazo
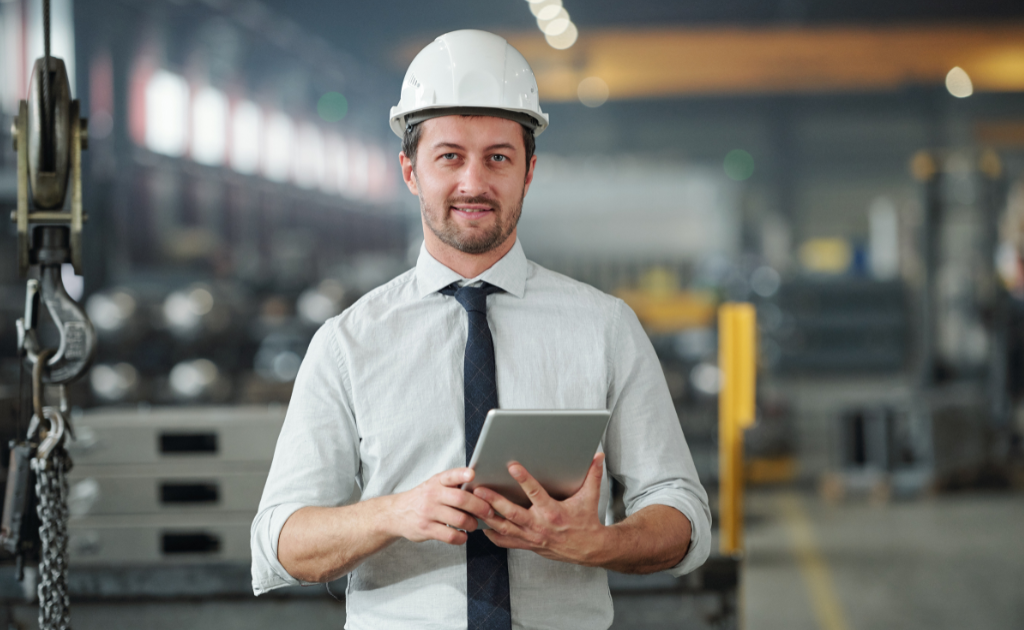
En cuanto a mantenimiento, el heat tracing eléctrico presenta menos requerimientos de intervención si está bien instalado.
Su talón de Aquiles suele ser el aislamiento dañado o la pérdida de continuidad del cable calefactor, pero estas fallas pueden detectarse con pruebas periódicas de megadohmios o verificación térmica.
Por su parte, los sistemas de vapor requieren inspección frecuente de válvulas, trampas y líneas de retorno de condensado.
Las fugas de vapor no solo desperdician energía, sino que también pueden afectar la seguridad y el rendimiento térmico. Además, encontrar la fuente de una fuga puede ser complejo y costoso.
En operaciones con alta carga de trabajo o ubicadas en regiones remotas del Perú, donde los desplazamientos del personal técnico son limitados, esta diferencia en mantenimiento puede inclinar la balanza a favor del sistema eléctrico.
4. Costo total de propiedad e infraestructura requerida
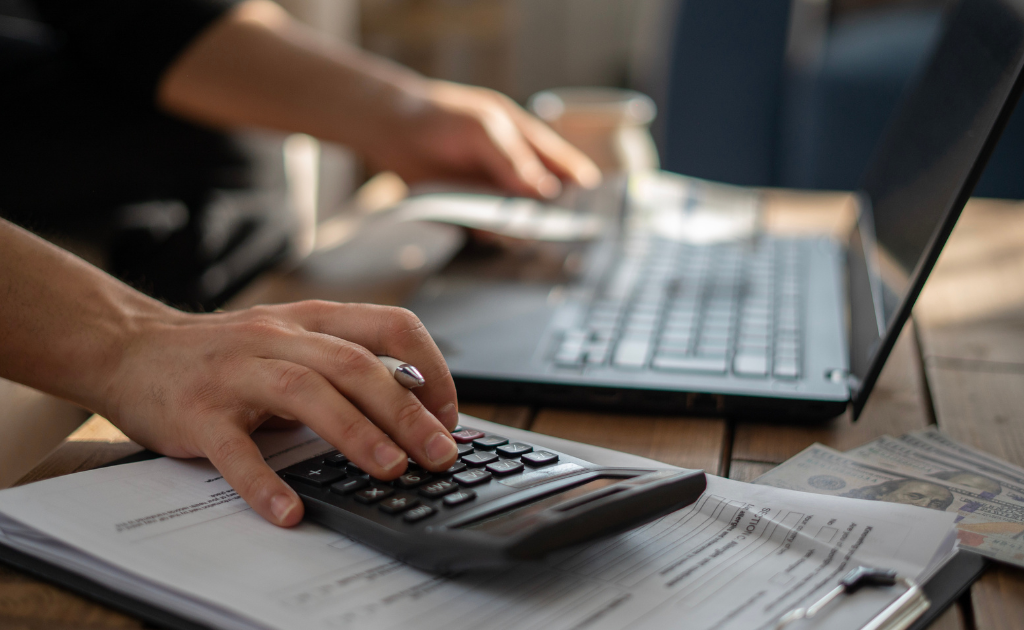
El análisis económico no se reduce al costo de adquisición. El vapor requiere una infraestructura robusta: calderas, líneas de distribución, trampas, válvulas y sistemas de retorno.
Estos elementos, además de costosos, requieren espacio, supervisión constante y materiales resistentes a la presión.
En cambio, los sistemas eléctricos de trazado térmico solo requieren una fuente eléctrica, controladores y cableado.
Aunque su inversión inicial por metro puede ser mayor, esta se compensa en muchos casos con menores costos de instalación, menores pérdidas térmicas y reducción del personal de mantenimiento.
La elección dependerá del contexto: si la planta ya cuenta con calderas y vapor disponible como subproducto, su uso puede ser rentable.
Pero si se trata de una instalación nueva o ubicada en zonas donde la energía eléctrica está más disponible, el trazado eléctrico representa una inversión más práctica y escalable.
5. Seguridad en zonas peligrosas y ambientes explosivos
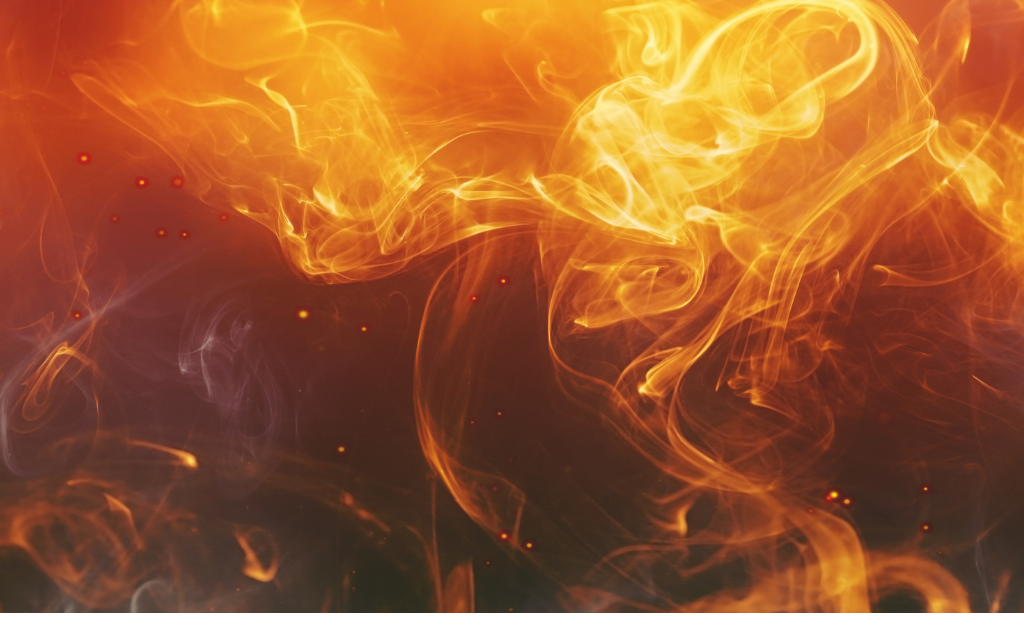
En entornos con riesgo de explosión, como plantas de gas o químicos, el vapor ofrece una ventaja clave: no genera chispas ni requiere componentes eléctricos dentro de la zona peligrosa, por lo que es considerado intrínsecamente seguro.
No obstante, los sistemas eléctricos también pueden ser instalados en zonas ATEX siempre que se utilicen componentes certificados, como cables con protección mecánica, cajas antideflagrantes y controladores aprobados para atmósferas peligrosas.
En Perú, donde la normativa está alineada con estándares internacionales, se pueden emplear ambas tecnologías de forma segura, siempre que se respeten los requisitos técnicos y de diseño de cada entorno.
Conclusión
Tanto el heat tracing eléctrico como el vapor pueden cumplir con los requerimientos térmicos más exigentes de la industria peruana, pero sus diferencias técnicas, logísticas y operativas deben ser cuidadosamente consideradas.
Los cables calefactores ofrecen precisión, control y menores costos operativos a largo plazo, mientras que el vapor sigue siendo una solución potente cuando se requiere calentamiento inicial rápido o cuando ya se cuenta con infraestructura disponible.
En proyectos de alta temperatura o aplicaciones críticas, el mejor camino no siempre es elegir uno u otro de forma absoluta, sino realizar un análisis de ingeniería para determinar qué solución —o combinación de ambas— entrega el mejor rendimiento técnico, económico y de seguridad para la planta y su entorno.