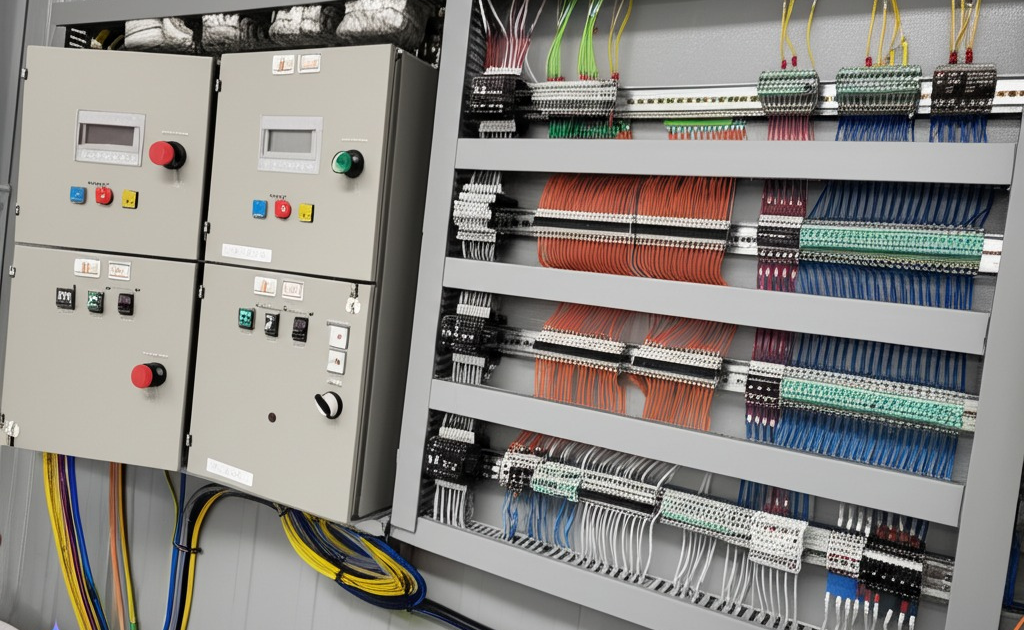
Tabla de Contenidos
- Introducción
- ¿Cómo calcular la longitud de cable calefactor necesaria?
- ¿Qué potencia por metro debo elegir según mi aplicación?
- ¿Cuántos circuitos debo dividir en un sistema de heat tracing?
- ¿Cómo seleccionar el controlador adecuado según la longitud del sistema?
- ¿Qué otros factores influyen en el dimensionamiento del heat tracing?
- Conclusión
Introducción
Seleccionar y dimensionar un sistema de heat tracing correctamente es fundamental para garantizar un funcionamiento eficiente y evitar problemas como sobrecalentamiento, consumo energético excesivo o insuficiente generación de calor.
En Perú, donde la minería, la industria petroquímica y el procesamiento de alimentos requieren control preciso de temperatura en tuberías y tanques, es común preguntarse cuántos metros de cable calefactor se necesitan, qué potencia es la adecuada y cómo estructurar los circuitos eléctricos.
En este artículo respondemos cinco preguntas clave sobre dimensionamiento, proporcionando reglas generales y consejos prácticos que ayudarán a ingenieros y técnicos a diseñar sistemas eficientes y seguros.
1. ¿Cómo calcular la longitud de cable calefactor necesaria?
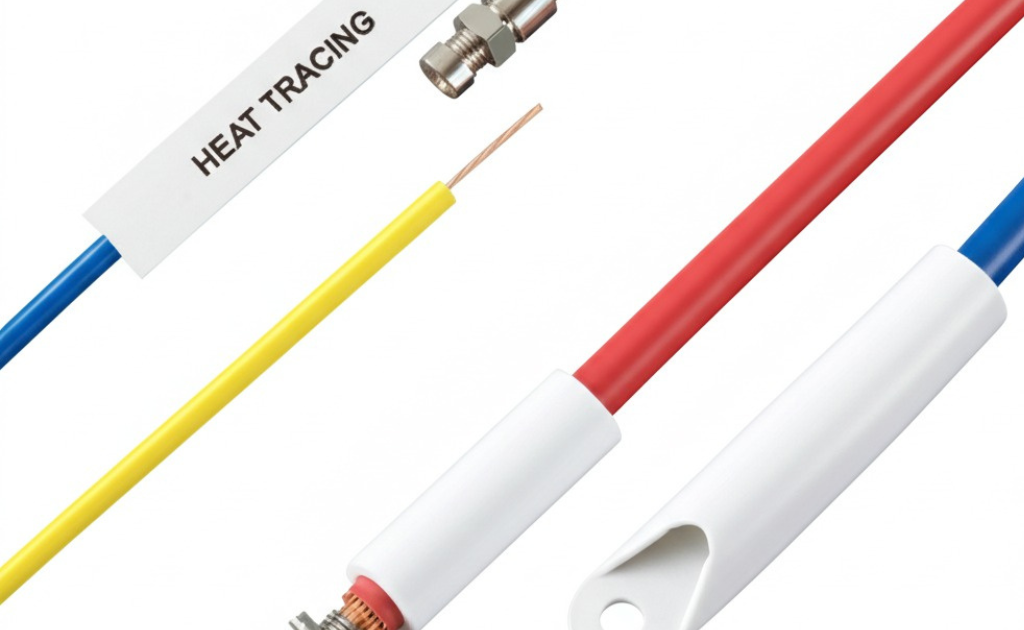
El cálculo de la longitud del cable calefactor depende del diámetro de la tubería, la forma de instalación y el método de cobertura térmica.
Para una instalación en línea recta, la longitud del cable es igual a la longitud de la tubería. Sin embargo, en aplicaciones que requieren trazado en espiral o cobertura adicional en válvulas y accesorios, la longitud del cable se incrementa.
La fórmula básica para estimar la longitud del cable es: L=F×LtL = F \times L_tL=F×Lt
Donde:
- LLL es la longitud total del cable calefactor (m).
- FFF es el factor de instalación (depende del método de trazado).
- LtL_tLt es la longitud de la tubería a calentar (m).
Para un trazado recto, el factor FFF es 1. Para instalaciones en espiral en tuberías pequeñas, puede variar entre 1.3 y 1.6. Si la tubería incluye muchas válvulas o accesorios, se recomienda agregar 10-15% más de cable para compensar las pérdidas de calor adicionales.
2. ¿Qué potencia por metro debo elegir según mi aplicación?
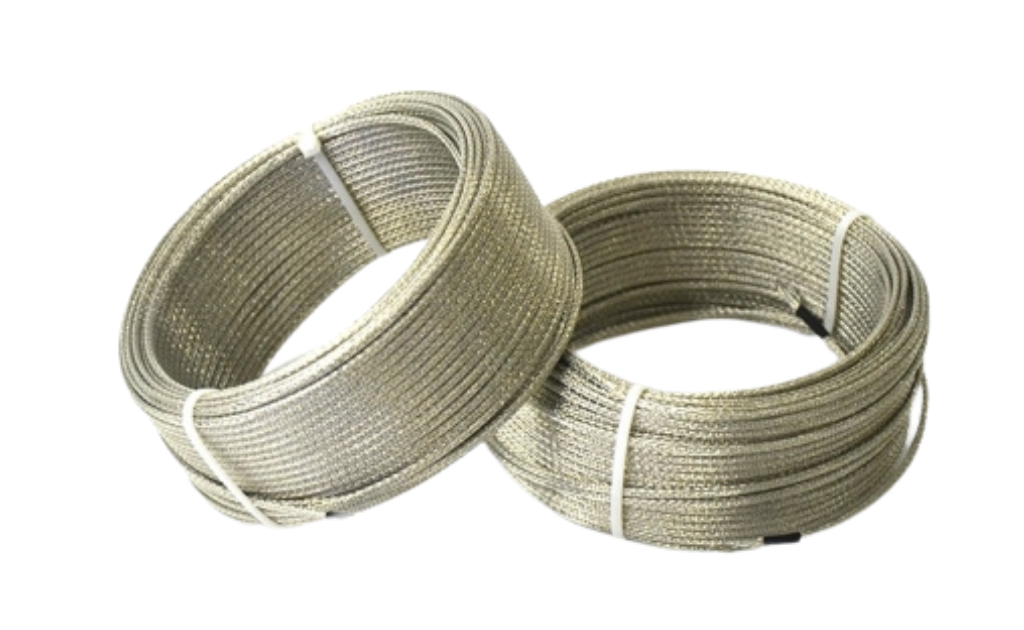
La potencia requerida por metro de cable calefactor depende de la temperatura de mantenimiento, la temperatura ambiente más baja y el aislamiento térmico de la tubería o tanque.
Para calcular la potencia necesaria (W/m), se utiliza la ecuación: P=QEfP = \frac{Q}{E_f}P=EfQ
Donde:
- PPP es la potencia del cable calefactor en W/m.
- QQQ es la pérdida de calor (W/m), calculada en función del diámetro de la tubería y el aislamiento.
- EfE_fEf es el factor de eficiencia (entre 0.9 y 1.1).
Ejemplo de selección de potencia según la aplicación:
- Protección contra congelamiento en tuberías pequeñas: 10-15 W/m.
- Mantenimiento de temperatura en procesos industriales: 20-30 W/m.
- Aplicaciones de alta temperatura en minería o petroquímica: 40 W/m o más.
En climas fríos como los de Cusco, Arequipa o zonas mineras altoandinas, se recomienda sobredimensionar la potencia para garantizar una temperatura estable en las tuberías.
3. ¿Cuántos circuitos debo dividir en un sistema de heat tracing?
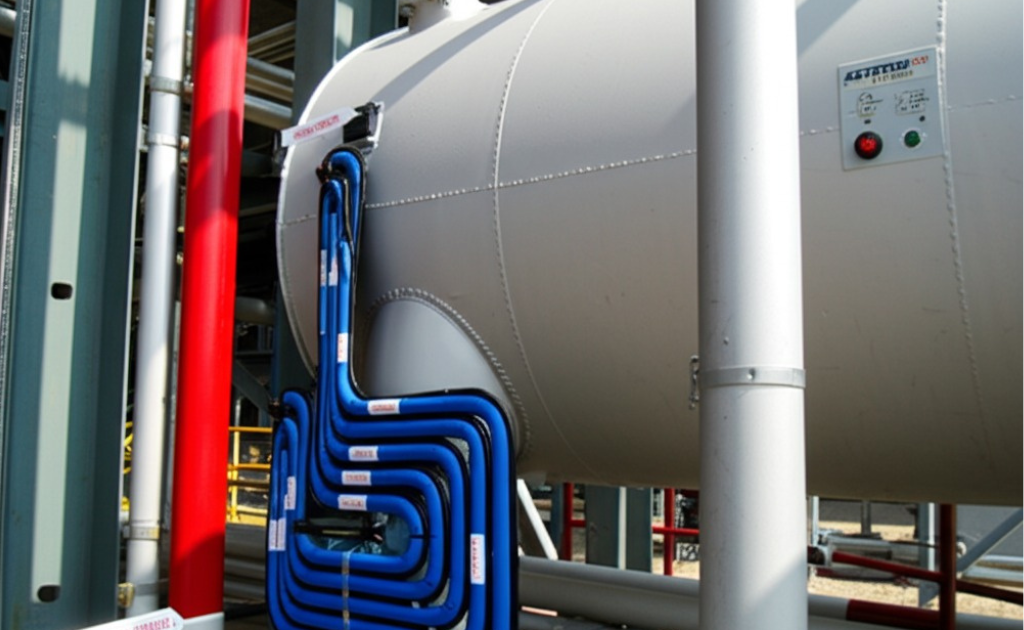
El número de circuitos en un sistema de heat tracing depende de la longitud total del cable calefactor y la capacidad de carga del suministro eléctrico.
Cada circuito tiene una capacidad máxima de longitud, determinada por la tensión de alimentación y la corriente que puede manejar el sistema. Un cálculo aproximado es: Lmax=V×IPL_{max} = \frac{V \times I}{P}Lmax=PV×I
Donde:
- LmaxL_{max}Lmax es la longitud máxima del cable en un solo circuito (m).
- VVV es la tensión de alimentación (V).
- III es la corriente máxima permitida en el circuito (A).
- PPP es la potencia por metro del cable (W/m).
Ejemplo: En un sistema de 240V con cables de 20 W/m y una capacidad de 20A por circuito, la longitud máxima de un solo circuito sería: Lmax=240V×20A20W/m=240mL_{max} = \frac{240V \times 20A}{20W/m} = 240mLmax=20W/m240V×20A=240m
Si la instalación requiere 500 metros de cable calefactor, se deben dividir en dos o más circuitos para no sobrecargar el sistema.
4. ¿Cómo seleccionar el controlador adecuado según la longitud del sistema?

El controlador de temperatura es un elemento clave en el diseño de un sistema de heat tracing, ya que regula el encendido y apagado del sistema según la temperatura de la tubería o tanque.
Los factores para elegir un controlador incluyen:
- Número de circuitos a controlar: Existen controladores individuales para pequeños sistemas y modelos avanzados para monitorear múltiples circuitos.
- Tipo de sensores compatibles: Se deben elegir sensores PT100 o termopares según la precisión deseada.
- Capacidad de integración con sistemas SCADA o BMS: En instalaciones industriales, es recomendable un controlador con monitoreo remoto.
Para sistemas extensos en plantas de procesamiento de líquidos o minería, se recomienda un controlador con alarmas de falla y monitoreo remoto, permitiendo una supervisión constante del rendimiento térmico.
5. ¿Qué otros factores influyen en el dimensionamiento del heat tracing?
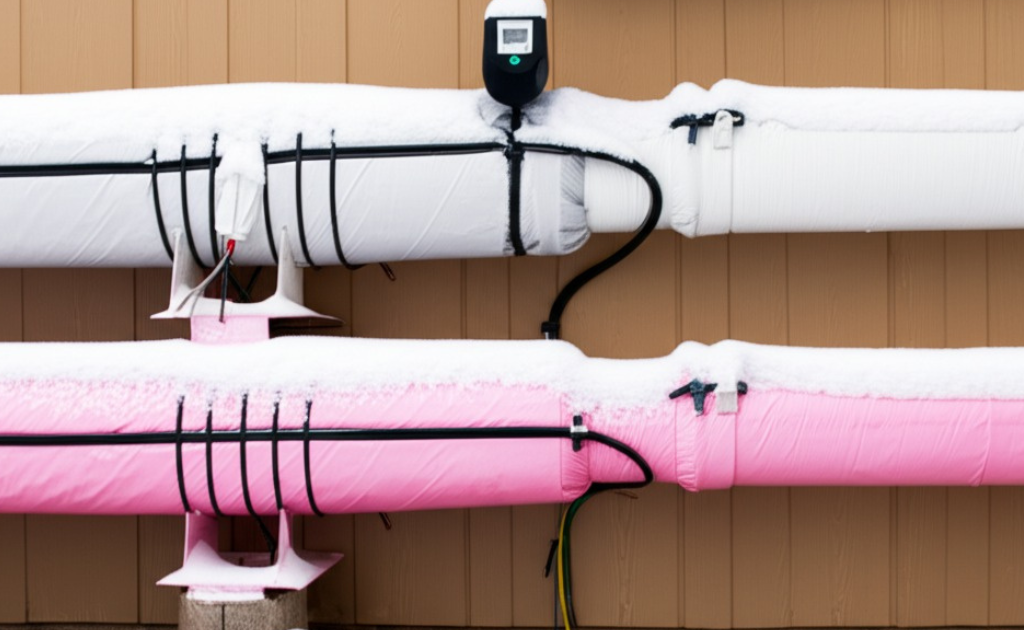
Además de la longitud, potencia y número de circuitos, hay otros aspectos a considerar en el diseño del sistema:
- Condiciones ambientales: En minas de gran altitud en Perú, la baja temperatura y la menor densidad de aire pueden afectar la eficiencia térmica.
- Tipo de aislamiento térmico: Un buen aislamiento reduce la pérdida de calor y permite usar cables de menor potencia.
- Exposición a químicos o abrasión: En entornos industriales agresivos, se deben usar cables calefactores con recubrimientos especiales resistentes a la corrosión.
- Normativas de seguridad: En zonas clasificadas (ATEX), es obligatorio el uso de cables y controladores certificados para evitar riesgos de ignición en atmósferas explosivas.
Estos factores influyen en la selección del sistema de heat tracing más adecuado para cada industria, garantizando una operación segura y eficiente.
Conclusión
El dimensionamiento de un sistema de heat tracing en Perú requiere una evaluación detallada de la longitud del cable, la potencia requerida, el número de circuitos y el tipo de controlador.
Cada aplicación es única, por lo que es fundamental utilizar fórmulas de cálculo, considerar las condiciones ambientales y seleccionar los componentes adecuados para garantizar un sistema eficiente y seguro.
Para aplicaciones en minería, alimentos, petróleo o tratamiento de aguas, comprender estos principios básicos de diseño ayuda a reducir costos, optimizar el consumo energético y evitar fallos operativos en entornos industriales exigentes.